1. 西门子软件如何实现虚实融合的工业革命?
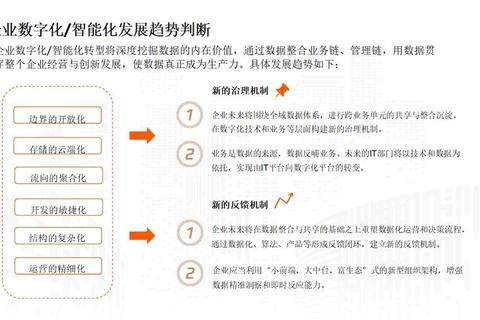
数字化浪潮下,一个争议性问题浮出水面:传统工业如何突破物理与虚拟的界限,实现真正的智能化?西门子用“数字化双胞胎”技术给出了答案。通过将物理设备与虚拟模型实时同步,企业可以在虚拟环境中模拟生产全流程,提前预判风险并优化效率。
以西门子Xcelerator平台为例,其数字化双胞胎技术已应用于汽车制造领域。某德国车企通过该平台对电动汽车生产线进行仿真,将原本需要6个月的调试周期缩短至3周,研发成本降低40%。而在疫苗生产领域,BioNTech借助西门子的Opcenter平台实现快速扩产,疫苗产能提升至传统模式的3倍,这正是虚实融合带来的革命性突破。
2. 生态整合:西门子如何打破数据孤岛?
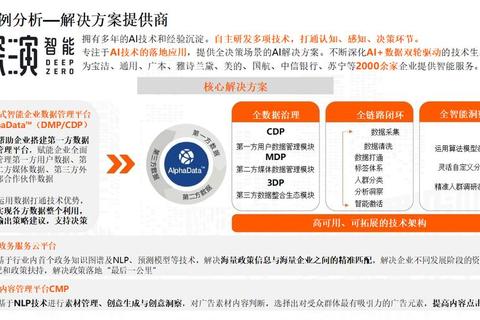
“数据孤岛”是工业数字化转型的最大阻碍之一。西门子MindSphere工业物联网平台的生态构建模式,成为破解这一难题的关键。通过AWS云服务,MindSphere连接了全球80%的工业自动化设备,实现跨品牌、跨协议的数据互通。
苏州金融租赁公司(苏州金租)的案例极具代表性。通过与西门子合作开发的智能租后管理平台,该企业将分散的租赁物数据统一接入云端。疫情期间,平台实时监控设备运行状态,远程生成数据报表,人工巡查频率降低70%,运营成本节约超500万元/年。这种“数据中台+行业应用”的模式,正是西门子生态整合能力的体现。
3. 复杂场景下,软件如何驱动生产力跃升?
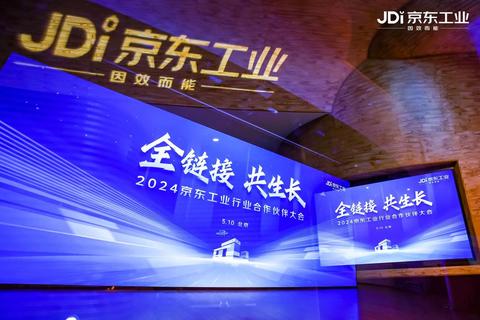
面对个性化定制与规模化生产的矛盾,西门子Tecnomatix解决方案展现了惊人的适应性。在西门子成都数字化工厂,370名员工管理着5条柔性生产线,通过PLM(产品生命周期管理)与MES(制造执行系统)的深度集成,实现PLC、人机界面等产品“零缺陷”交付,人均产值达行业平均水平的2.5倍。
更极致的案例来自武汉变压器厂。引入西门子轻量化数字工具后,该厂打通20余个数据系统,设备利用率从65%提升至89%,疫情期间10天内产能恢复100%。其核心在于知识图谱技术的应用——将工程师经验转化为可复用的算法模型,让“在家造变压器”成为可能。
--
可操作建议
企业若想借力《高效能西门子软件引领数字化创新浪潮》,可分三步走:
1. 诊断先行:参考西门子“EAD战略”(电气化-自动化-数字化),从价值链痛点切入规划转型路径;
2. 场景验证:选择1-2个关键环节部署MindSphere或Xcelerator,通过“小步快跑”验证价值;
3. 组织变革:参与西门子“数字化企业领军项目”培训,同步升级人才体系与考核机制。
这场由《高效能西门子软件引领数字化创新浪潮》驱动的变革,已不仅是技术升级,更是工业文明向智能文明跃迁的必由之路。正如西门子成都工厂的实践所示——当物理世界与数字世界深度交织,生产效率的指数级增长将成为新常态。
相关文章:
文章已关闭评论!