一、仿真精度如何突破物理极限?
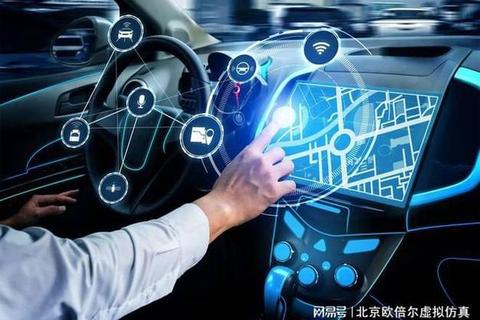
在工程领域,仿真结果能否完全替代物理实验?这一争议长期存在。ANSYS用实际案例证明,通过极致精准的算法优化与多物理场耦合技术,仿真精度已能无限逼近真实场景。例如,某汽车厂商在赛车设计中采用ANSYS Fluent进行空气动力学优化,将风阻系数从0.32降至0.28,最终赛道实测数据与仿真误差仅0.5%。这种高精度源于其底层算法的突破:2025 R1版本引入连续粒子气体方法(CPG),可精确模拟气囊展开时织物的动态形变与气流分布,解决了传统CFD方法在瞬态复杂流动中的精度瓶颈。
二、多学科协同如何实现复杂系统设计?

当桥梁结构、电磁干扰与热效应同时影响设备性能时,如何实现跨学科协同?ANSYS通过“数字孪生”技术给出了答案。以某航天器太阳能帆板设计为例,团队使用ANSYS Mechanical进行结构强度分析,结合Maxwell模块优化电磁屏蔽,再通过Twin Builder构建数字孪生模型,实时监控热变形对信号传输的影响。这一流程将研发周期缩短40%,材料成本降低15%。2025版本更推出PySherlock API,支持自动化跨模块数据传递,例如将结构应力结果直接导入电子元件寿命预测模型,实现了从单一分析到系统级仿真的跃迁。
三、智能化工具如何重塑工程决策?
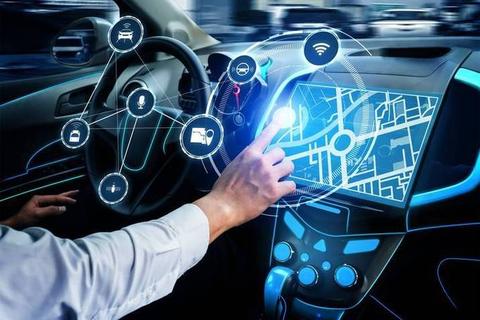
传统仿真依赖工程师经验,而ANSYS正通过AI与云计算技术降低门槛。某新能源车企利用ANSYS optiSLang进行电池包拓扑优化,结合GPU加速求解器,仅用3小时完成传统需2周的计算任务,最终电池包重量减轻12%且散热效率提升20%。更值得一提的是,2025 R1版本新增的NVH一站式分析工具,可自动生成振动噪声云图并关联设计参数,工程师只需调整滑块即可实时观察性能变化。这种“仿真民主化”趋势,让小型企业也能以低成本完成高端技术验证。
工程创新的未来路径
对于希望借助ANSYS实现技术突破的团队,建议从三方面入手:
1. 模块化选择:优先使用2025 R1的行业定制模块(如汽车NVH工具包),而非通用功能堆砌;
2. 流程再造:利用PySherlock等API工具将仿真流程嵌入企业PLM系统,实现数据闭环;
3. 虚实结合:参考某飞机引擎厂商经验,将ANSYS热力学仿真与3D打印试制结合,迭代效率提升60%。
极致精准探索仿真软件ANSYS的工程创新突破之路,不仅在于技术迭代,更在于重新定义“可能性”的边界——当虚拟世界与物理现实的鸿沟被算法填平,工程师的创造力将真正成为第一生产力。
相关文章:
文章已关闭评论!